Huge investments and cutting-edge research are helping China to pioneer innovations in clean energy technologies, reports Mark Peplow
An energy revolution is in full swing an hour’s drive from the centre of Dalian, a sprawling city in north-east China. Inside a pristine new factory on an isolated industrial estate, the world’s biggest battery is taking shape.
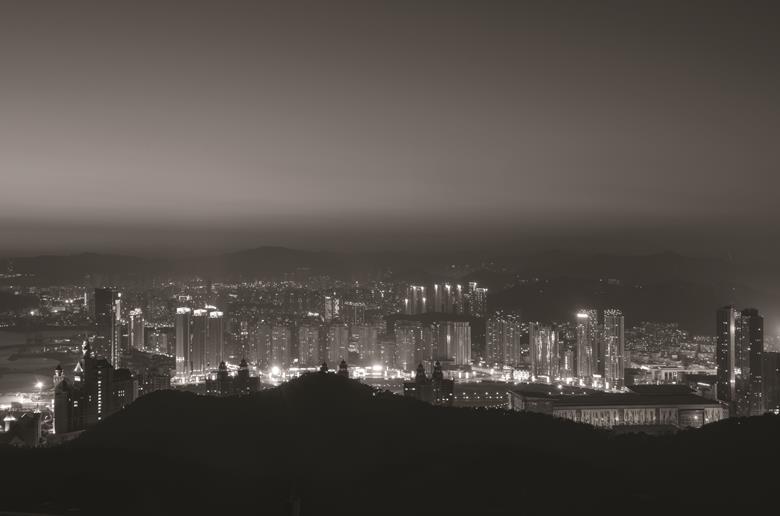
Keeping the lights on in Chinese cities like Dalian might soon be little more sustainable. (Photo by iStock/Getty Images)
Out in the back lot, swaddled under blue tarpaulin sheets, are about 120 shipping containers. Each of them carries the guts of a battery capable of storing around 1MWh of energy, at least a dozen times more than a fully charged electric car. Soon, these containers will be transported along the coast to join an enormous array, which will be fed by the windfarms that dot the Dalian peninsula. By 2019, this behemoth battery will have enough containers to store an unprecedented 800MWh.
This not only dwarfs a high-profile 129MWh lithium-ion battery facility being built by electric-car maker Tesla in Jamestown, Australia. It also relies on a completely different technology: these are vanadium flow batteries (VFBs), which store and release energy through a redox see-saw of dissolved vanadium ions.
Go with the flow
The 2.9 billion yuan (£330 million) project is one of about 30 battery installations being built across China by Rongke Power, a spin out of the Dalian Institute of Chemical Physics (DICP). Business is booming thanks to a unique blend of science and policy. In September 2017, China’s economic planning agency called for a huge increase in grid-scale energy storage facilities, including VFBs, in order to flatten the peaks and troughs in supply from intermittent renewable sources. The government now requires renewable energy companies to install energy storage facilities alongside new solar or wind generating capacity.
But VFBs have also benefitted from Chinese research in chemistry and materials science, which has been crucial to improving their performance and driving down costs. ‘In vanadium flow batteries, China is leading the world,’ says Huamin Zhang of the DICP, co-founder and chief engineer at Rongke Power.
There is an oft-repeated cliché that China is much better at adopting technologies invented in other countries than it is at domestic innovation. That may once have been true, says Pierre Verlinden, chief scientist at Chinese solar energy company Trina, based in Changzhou: ‘But now it’s a myth.’
China has established a growing number of clean energy research centres over the past decade, and their scientists are now doing cutting-edge research in areas from photovoltaics and batteries to CO2 capture and use. These discoveries are feeding through into commercial products at a remarkably rapid pace, thanks to staggering levels of financial support. The United Nations Environment Programme estimates that China invested $103 billion (£77 billion) in renewable energy in 2015, more than one-third of the world’s total.
This could have a profound impact on the global battle against climate change. China currently produces more than one-quarter of the world’s CO2 emissions, largely from its coal-fired power stations. But the country now aims to generate 20% of its electricity from non-fossil sources by 2030, and halve its greenhouse gas emissions from 2010 levels over the same period. It’s clear that reaching that goal will depend on advances in the chemical sciences: ‘The key to all of this is fundamental research,’ says Peter Styring, director of the UK Centre for Carbon Dioxide Utilisation at the University of Sheffield.
V for victory
Zhang founded Rongke Power in 2008, and its gleaming factory opened in November 2016. It is entirely powered by solar panels on its roof hooked up to VFBs, Zhang says proudly. Inside, employees work side by side with an army of robots to assemble and test the batteries’ cells, before loading them into the containers along with pumps, filters and a computerised control system.
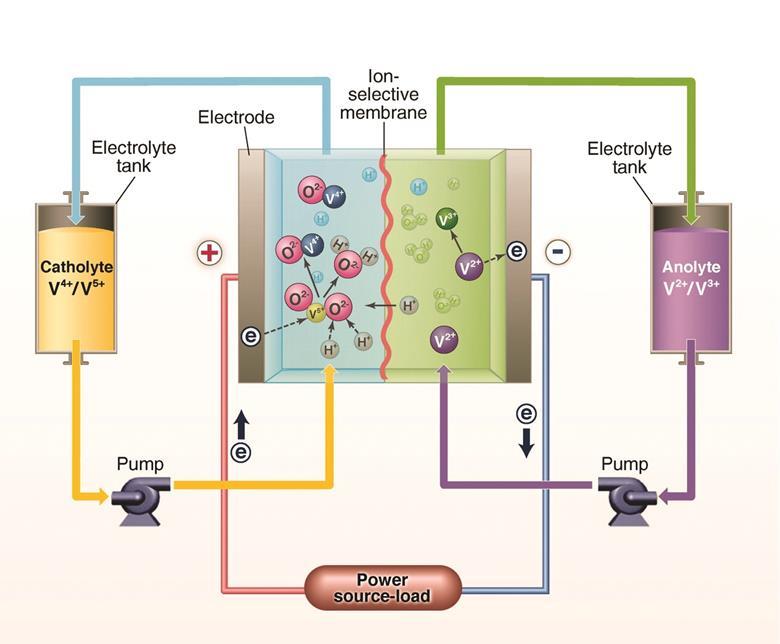
Vanadium flow batteries exploit the many oxidation states of the transition metal. (Image by 2011 AAAS)
Every container will be hooked up to a pair of 4m-high tanks, each holding 30m3 of vanadium salts dissolved in sulfuric acid. During operation, these electrolytes are pumped through a pair of half-cells separated by a proton exchange membrane. When the battery discharges, V2+ ions are oxidised to V3+ ions in one half-cell, releasing a flow of electrons; meanwhile, V5+ ions in the other half-cell are reduced to V4+ ions. (J. Phys. Chem. Lett.)
VFBs have some clear advantages over other batteries. They are easy to scale up — simply make the electrolyte tanks bigger, and they can store more energy. Stacking more cells together in the battery increases the overall power that it can deliver. Unlike most other batteries, these attributes can be changed independently, making it easier to tailor them to particular applications that may require a larger cache of energy, or a higher power output. And while lithium-ion batteries are typically guaranteed for only eight years, VFBs can last much longer. ‘A 20-year lifetime is not unusual,’ says George Crabtree, director of the Joint Center for Energy Storage Research at Argonne National Laboratory in the US.
Vanadium flow batteries were first developed in the 1980s, but Zhang’s team made several key innovations to improve their commercial prospects. One of the biggest barriers to scale-up was that VFBs typically used Nafion membranes, which are expensive and tended to get clogged with vanadium ions. So Rongke developed an alternative membrane based on a non-fluorinated polymer that is 80% cheaper than Nafion, and has smaller pores for better ion selectivity. That allows protons to speed through the membrane, doubling the current density across the cell to 160mA/cm2 and significantly improving the power output. (Energy Environ. Sci.) At the factory, robot arms in a sealed chamber swiftly cut these black, spongy membranes into 30cm × 75cm rectangles that are used in the cells. Further modifications to the material are expected to push their current densities past 200mA/cm2, says Xiaobo Xu, Rongke’s vice-general manager.
Meanwhile, the 2mm-wide bipolar plates that provide an electrical connection between neighbouring cells in the stack were previously made from expensive and brittle graphite. So Rongke created a highly conductive carbon-plastic composite plate that is cheap and flexible. ‘To see this go from basic research to commercialisation in 15 years is very satisfying,’ says Zhang.
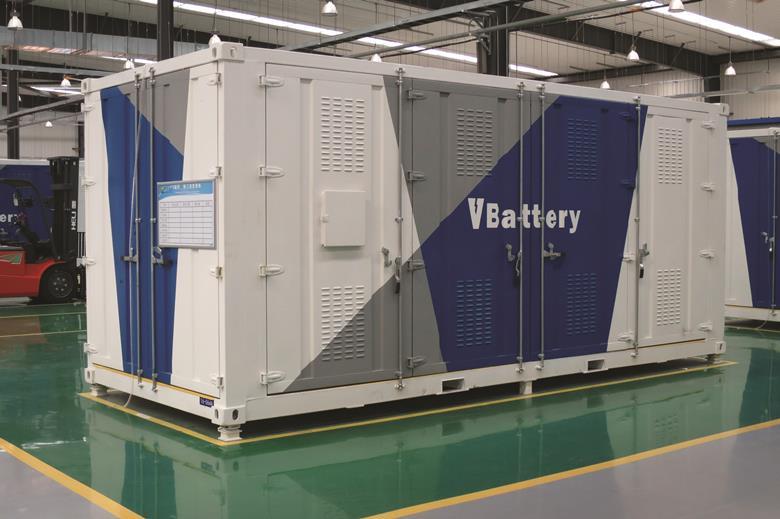
Rongke Power’s vanadium flow battery units are ready to store energy from renewable sources for when it is needed. (Photo by Rongke Power)
Dalian is an ideal place to build the battery array, he explains. Situated on a windy peninsula, about 15% of the region’s electricity comes from wind power, but there is only one land route to carry electricity from China’s power grid, so the region is vulnerable to power outages. ‘This battery can be used as an emergency power station for Dalian,’ says Zhang. Pumped hydroelectric power storage is less suitable, he adds, because there are relatively few large inland bodies of water in the region.
The company also has orders from energy companies in Germany and Italy, yet Crabtree is sceptical that VFBs will soon conquer the world. ‘They’re just too expensive,’ he says. A decade ago, VFB energy storage cost an estimated $1000 per kWh. Rongke’s improvements have halved the cost, and they aim to reach $300 per kWh in the next few years. But lithium-ion batteries have been getting cheaper too, with average prices falling from more than $500 per kWh to around $150 per kWh over the past five years.
Lithium-ion technology also has a much bigger market than VFBs because of its use in consumer devices and electric cars, and this has helped to hone the technology. Already a huge industry, it is now on the cusp of enormous growth, with Tesla’s Nevada-based Gigafactory and others springing up around the world. In contrast, says Crabtree, VFBs are limited to grid-storage applications, and are still something of an unknown quantity in the energy sector. ‘If you were driven only by economics, you wouldn’t install a flow battery at the moment,’ says Crabtree.
China, though, is not necessarily constrained by purely economic factors, and frequently takes top-down, political decisions about big infrastructure projects. It also helps that Chinese mines produce more than half of the world’s supply of vanadium. (Mineral Commodity Summaries)
Crabtree says that big demonstration projects like Rongke’s are vital to improving VFB technology, even if they are not currently the most economical solution. ‘That experience is crucial – at some point, you really just have to try it,’ he says. Meanwhile, Zhang believes that costs will fall once a second generation of VFBs is built. The electrolyte makes up about 40% of the battery’s capital costs, so when a VFB reaches the end of its lifetime, the vanadium can simply be transferred to a new unit, making it significantly cheaper. It’s a fair point, says Crabtree — but it will take decades to see whether it pans out.
VFBs are not the only game in town, though. ‘The country is trying to prioritise battery manufacturing as a strategic industry,’ says Anders Hove, an independent energy consultant based in Beijing. For example, Crabtree says that battery manufacturer BYD in Shenzhen has focused its efforts on lithium-ion batteries with iron phosphate cathodes. Although these have a lower power and energy density than rival lithium-ion batteries with cobalt oxide cathodes, they are also cheaper and last longer. ‘The Chinese are starting to make technology advances that lead to better batteries,’ says Crabtree.
Hove predicts that as Chinese manufacturers develop these battery technologies and scale up manufacturing, costs could fall dramatically. ‘People underestimate how cheaply they can be made in China,’ he says.
Solar success
There is already ample precedent for the impact of technological innovation and economies of scale on renewable energy. Just 10 years ago, photovoltaic (PV) power typically cost more than $5 per watt. This year, Chinese manufacturers will make silicon cells that produce electricity for less than $0.25 per watt. ‘That’s an enormous reduction in costs, and it has been enabled by research done in China,’ says Verlinden. His company, Trina, is one of the world’s biggest suppliers of PV cells, selling more than 23GW of modules in 2016, accounting for more than 10% of the global market.
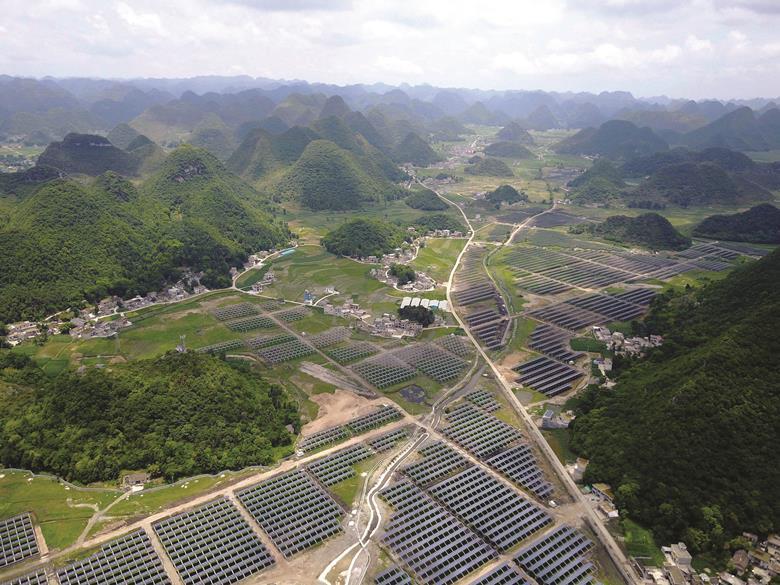
China is investing in solar in a big way, as these panels in Guizhou province show. (Photo by AFP/Getty Images)
Over the past decade, China’s PV manufacturing has ramped up at an astonishing rate as companies improved production processes and moved quickly to adopt the latest improvements in solar technology. China now makes most of the world’s solar PV modules, and by 2017 the global installed PV capacity had topped 300GW, supplying almost 2% of the planet’s electricity.
China is also installing far more solar panels than any other country. In 2016 alone, the country’s installed solar power capacity jumped from 43GW to 77GW. In December 2016, China announced a new five-year plan for solar energy that aims to reach 110GW of installed solar power by 2020. Yet in January 2018, analysts at Bloomberg New Energy Finance estimated that China had already installed enough PV capacity during 2017 to push it above that target.
And solar panels are no longer confined to large installations in the more rural northern and western provinces; now they are beginning to cover the rooftops of houses and businesses across the country, which makes for simpler electricity distribution. ‘There has been a dramatic increase in this “distributed” solar in China,’ says Hove.
Interestingly, China’s five-year solar energy plan singles out Perc (passivated emitter rear contact) cells as a key growth technology. These cells have a slightly different architecture to a standard PV, and contain a layer of insulating material, such as alumina, at the back of the cell. This helps to reflect unabsorbed light back into the semiconductor, improving the overall efficiency of the cell. China’s Perc cell manufacturing output is expected to rise from 15GW per year in 2016 to 61GW in 2020, by which time it should account for about 45% of the silicon solar cell market, according to market intelligence company EnergyTrend.
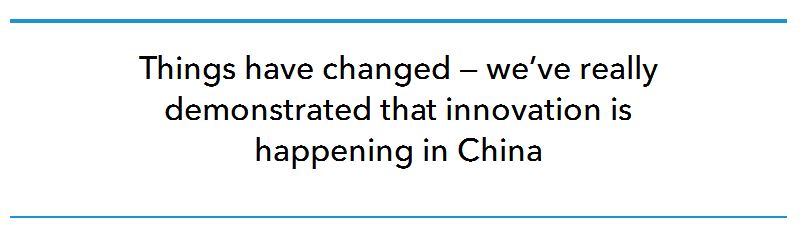
Perc cells were developed in the late 1980s, but took 30 years to reach widespread commercialisation as companies struggled to find the best way to deposit and shape the alumina layer. In 2016, Trina’s R&D division — designated by the government as the State Key Laboratory of PV Science and Technology of China — built a Perc cell with a record-breaking efficiency of 22.6%. Less than a year later, the model had gone into commercial production (commercial models typically offer about one percentage point less efficiency than lab champions).
Pushing PV efficiencies upwards depends on a range of incremental improvements, such as reducing contamination within the silicon to curb the recombination of electrons and holes, tweaking the cell’s components and adjusting manufacturing practices. ‘It’s thousands of little steps,’ says Verlinden.
The company also works on interdigitated back contact (IBC) cells, which offer more efficiency for a higher price — a good choice for cramped sites, says Verlinden. Conventional solar panels typically have a grid of wires on top of the cells to carry current, but these block some of the incoming light. IBC cells shift those electrodes to the back of the device to allow more light through, which boosts their efficiency but also makes manufacturing much more complex. ‘It’s expensive, so there’s no point in making a cell that doesn’t have a high efficiency,’ says Verlinden. So in 2017, the company unveiled an IBC cell that boasted a record efficiency of 24.1%. ‘You can’t do that by copying what other people do,’ he says. ‘A decade ago, there was very little research base here, so companies had to import the technology. But things have changed — we’ve really demonstrated that innovation is happening in China.’
Verlinden credits this success in part to the collaborative spirit that exists between PV researchers across academia and industry in China, who are enthusiastic users of the WeChat messaging app. ‘The entire PV industry communicates this way – I receive messages every five minutes or so,’ he says. ‘Someone presents slides somewhere in the world and two minutes later they’re on my phone. It is absolutely amazing. You have thousands and thousands of people working on the same processes, and they’re all collaborating.’
The next generation
The surge in silicon PV cells may, however, have a downside. The enormous investment in silicon cell production lines can make it harder for less resource-intensive thin-film PV technologies, such as cadmium telluride, to gain ground in the market.
But another burgeoning thin-film technology may avoid this problem of technological lock-in. Perovskite solar cells have had a meteoric rise over the past decade, with efficiencies rising from about 4% in 2009 to more than 22% in 2017. (Science) These cells rely on perovskite-structured materials such as methylammonium lead iodide to absorb light and generate a current, and they should be relatively cheap to manufacture by low-temperature solution processing. Crucially, their chemistry can be tuned to absorb a different part of the solar spectrum than silicon. That means a perovskite cell can be laid on top of a silicon cell to boost its overall output, a ‘tandem’ arrangement in which perovskite serves as an assistant rather than a commercial rival.
Chinese researchers are forging ahead with perovskites, and by 2015 had published almost one-quarter of all research papers on the technology, according to market intelligence company Lux Research. And they are already developing strategies for commercial perovskite cell production. If the cells were made in flexible form, for example, they could be manufactured using fast and efficient roll-to-roll production methods. With that goal in mind, a DICP team led by Shengzhong Liu recently developed a flexible perovskite cell with an energy conversion efficiency of 16%, the highest yet for a flexible perovskite. This record-breaking performance relies in part on using an ionic liquid to boost electron transport within the cell. (Adv. Mater.)
It’s clear that Chinese solar panel manufacturers are interested in perovskites, says Tyler Ogden, an analyst at Lux. ‘Given the potential for perovskite integration with their existing silicon assets, it is likely they are investigating tandem cells,’ he says.
The coal challenge
Despite its enormous progress in renewable energy, China is still addicted to coal. It has more than 900GW of coal-fired power stations, generating about two-thirds of China’s electricity — and more than 80% of its CO2 emissions. Although coal consumption in China declined for the first time in 2015, an additional 200GW of coal-power capacity is planned by 2020, and projections suggest that coal will still produce well over half of China’s energy by 2030.
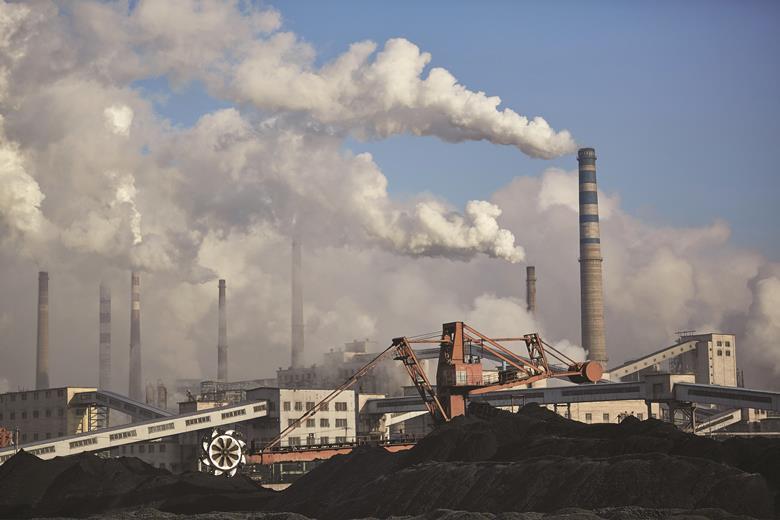
Although efforts are being made to move away from coal power, it will take a long time for China to wean itself off the black stuff. (Photo by Christian Petersen Clausen/Moment/Getty Images)
But not all of it is burned. Given the country’s relatively limited oil resources, coal has also become a vital feedstock for the chemicals industry. Coal is typically treated with oxygen and steam to produce syngas, a mixture of hydrogen and carbon monoxide. Syngas can then go through the Fischer–Tropsch process to make liquid hydrocarbon fuels, for example, or produce key chemicals like methanol.
So the country is investing heavily in carbon capture, utilisation and storage (CCUS) — the technologies that can grab CO2 released by fossil fuels, and then use it as a chemical feedstock, or store it in underground rock formations. ‘We see China as a fast-developing future leader in this field, simply because of the amount of resources they’re putting in,’ says Styring.
In 2017, construction began on the Yanchang Integrated CCS Demonstration facility in Yulin City, which aims to capture about 400,000 tonnes of CO2 per year from two coal-to-chemicals plants. The CO2 will then be pumped into the Qiaojiawa oilfields to help recover oil. China has seven more CCS projects in the early stages of development, and is expected to become a key player in the area over the next two decades. ‘If CCS is widely deployed anywhere, it’ll be in China,’ says Tristan Stanley, an analyst with the International Energy Agency in Paris, France.
The typical capture process currently uses solvents such as monoethanolamine that react with CO2 to form C–N bonds; these are subsequently broken apart at 100–120°C to release purified CO2 that is suitable for storage or utilisation. One of the big challenges is that the temperature swings involved in capturing, separating and releasing CO2 in this way make it a very expensive process, costing $50–100 per tonne of CO2 and consuming 25–40% of the energy generated by the plant. This effectively doubles the cost of the electricity it produces.
So researchers are investigating a range of other ways to capture CO2 with a lower regeneration cost, such as porous materials that can physically adsorb CO2 and then release it under much milder conditions. For example, a team led by Shuixia Chen at Sun Yat-Sen University in Guangzhou has developed a series of porous polyamine materials that readily adsorb CO2 at room temperature, and then desorb the gas at 90°C. (Sci. Rep.) Others are investigating metal–organic frameworks (MOFs), highly porous materials made from metal-based nodes held together by organic struts or linkers. One advantage of MOFs is that their structures and chemical activities are highly tunable, so it should be possible to design materials that bind CO2 sufficiently well to separate it from a gas stream, but that also release the CO2 without extreme heating. Using these sorts of design principles, Jie-Peng Zhang and colleagues at Sun Yat-Sen University found that a cobalt-azolate MOF known as MAF-X27ox had the highest uptake of CO2 by volume of any MOF, and also released it rapidly at a relatively mild 85°C. (Energy Environ. Sci.)
Once CO2 has been captured, says Styring, storing it underground should be a last resort: ‘It’s basically landfill disposal.’ A much better option is to transform the CO2 into useful chemicals, he says, adding that ‘a huge amount of effort is going into CO2 utilisation in China’.
Some of China’s leading work in this area is happening in Dalian. At its campus in downtown Dalian, the DICP is home to the Dalian National Laboratory for Clean Energy (DNL), which opened in 2011. ‘It was China’s first national laboratory in the field of clean energy research,’ says Yuqi Jin, vice-director of the DICP.
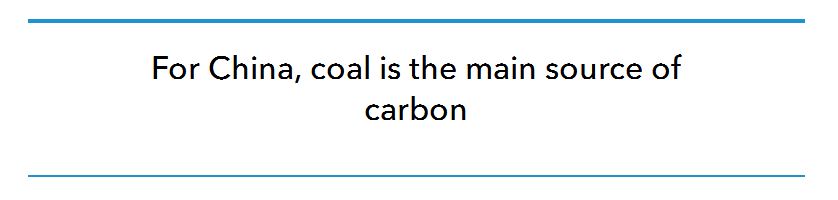
In October 2017, a team led by the DNL’s director, Can Li, unveiled a zinc oxide–zirconium oxide catalyst that converts hydrogen and CO2 to methanol. (Sci. Adv.) Previous catalysts for this reaction had suffered from poor methanol selectivity – producing a messy mixture of products – or deactivated rapidly. In contrast, the bimetallic catalyst remained stable for more than 500 hours, and ensured that 90% of the product was methanol. One reason for this success, says Li, is that the two metals have different functions: zinc binds H2, while neighbouring zirconium binds and activates CO2. ‘China is making big advances in CO2 to methanol,’ says Styring.
Meanwhile, the DNL’s Jian Sun and Qingjie Ge led a team that developed a catalyst that could turn CO2 and hydrogen into gasoline-range hydrocarbons. The catalyst is composed of iron oxide nanoparticles, their surfaces peppered with sodium atoms, which were loaded into a zeolite. This effectively provides three different catalytic sites where the CO2 is first reduced to CO, then hydrogenated to produce olefins, and finally coupled together inside the zeolite. (Nat. Commun.) Styring says that this kind of chemistry is booming in China: ‘There’s a huge market out there for synthetic fuels.’
Styring acknowledges that, from an environmental point of view, it would be better to simply leave the coal in the ground. But China is the world’s largest coal producer, and still heavily reliant on the fuel, so a sudden halt to coal mining is unrealistic. ‘For China, coal is the main source of carbon — whether for energy or chemicals — and it is still heavily invested in using that domestic resource,’ says Stanley.
Nevertheless, there can be a gradual shift in how the coal is used. ‘If you take the coal and produce syngas, you have a feedstock for the chemical industry,’ says Styring. ‘While that’s not a complete removal of fossil carbon, it puts it to a better use from an environmental point of view, because you’re displacing fossil fuels from the supply chain.’ Given China’s progress in this field, Styring says that it is essential for researchers around the world to collaborate with scientists there to advance these technologies. ‘I’m treating it as a high priority,’ he says.
‘In the long term, the government sees this as a good way to reduce CO2 emissions at a large scale,’ says Tony Zhang of the Global CCS Institute, an advisory and advocacy group based in Melbourne, Australia. ‘And the government has been quite generous in terms of funding support,’ he adds. ‘In fundamental research, China is catching up quickly.’ (Chemistry World)
2018.03.13